Case Study 2 – Burdensome Supply Management
The Problem
Operating a sizeable office building is not as simple as it looks. This was especially true for an office building owner when it came to maintaining supplies like paper towels, soap, toilet paper and other items that you never want to be without. To ensure seamless availability of supplies, he needed a system to handle the inventory and ordering processes.
The User’s Solution
At his building, he used paper forms to complete a weekly inventory of supplies. This took about an hour and a half to complete, followed by entry into an Excel sheet to compare stock on hand to reorder points. Then the quantities to be ordered had to be determined before purchase orders could be written and sent to his two preferred vendors. It was obvious to him that the time involved in doing this was excessive and costly.
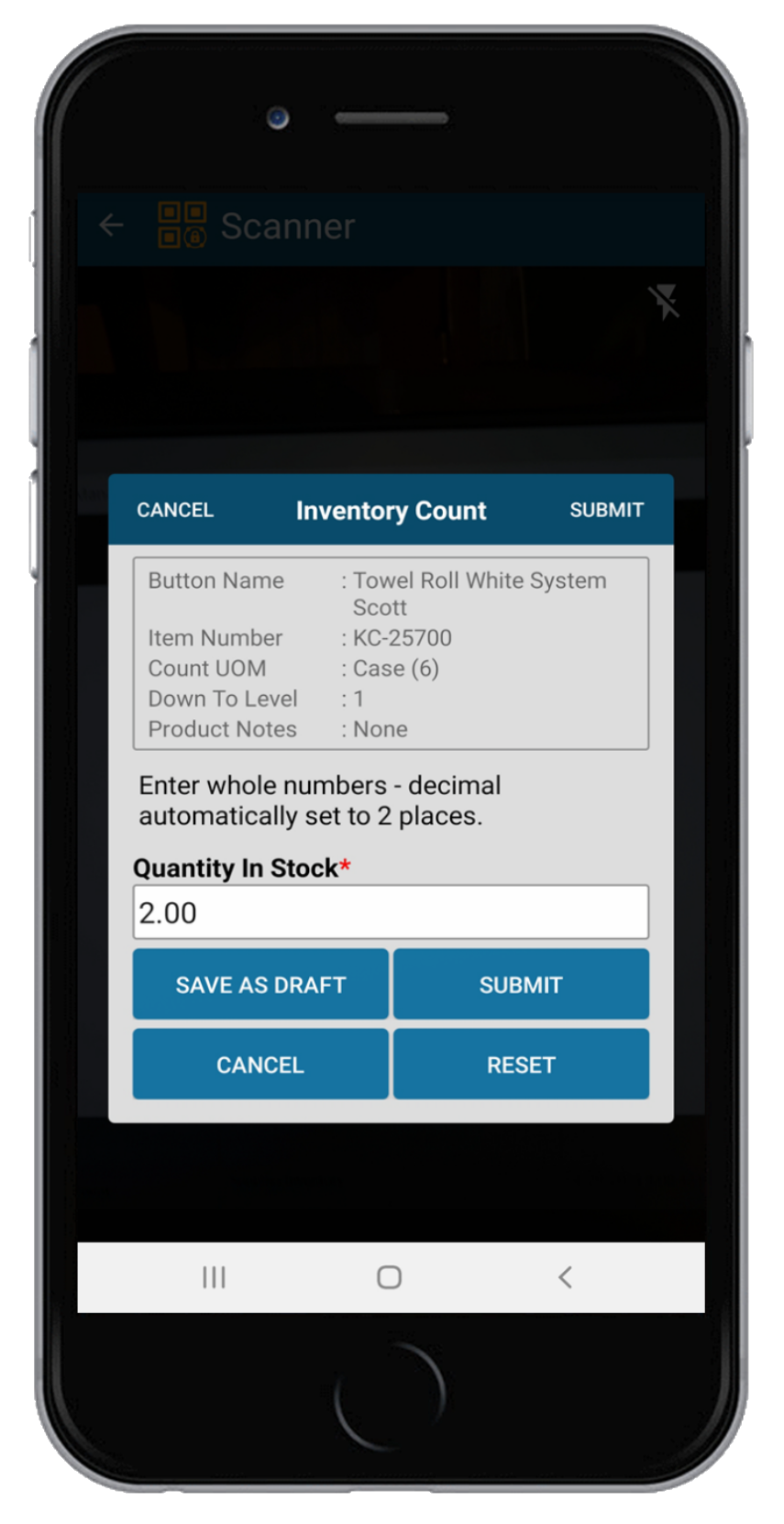
The FormsTrackR Solution
When the building owner moved to FormsTrackR, he created QR codes for every product, placed them on the shelves in the appropriate places so they could be scanned with a smartphone. Now a product-specific form pops up, the quantity on hand is entered, and the data is ported to a report that contains information about reorder point thresholds, minimum order quantities and ordering units such as single units, cartons of multiple units, and so forth. By adding logic to the report, the order is now automatically calculated based on the appropriate ordering formula for each product, and a separate order is created for each vendor. Another exception report lists any products that were not entered into the weekly inventory so that someone can go back and add them to the reports and orders if needed. Finally, reports are automatically generated listing products to be ordered. The orders were also set to be automatically emailed to the vendors once approved.
What Was Saved?
- The building owner now saves almost 1-1/2 hours every week when performing the inventory and there are no forms to print.
- More importantly, the exception report ensures that he knows if product was not counted, something that was easily overlooked in the past with the manual system.
- The savings from avoiding emergency orders is truly priceless.
What Was Improved?
- In addition to the time saved in performing inventories, the ability to automate the ordering process accurately with no user intervention has streamlined and improved the building operations immeasurably.
- Additionally, reports can be created to analyze supply usage trends as well as determine if theft or abuse may be occurring when spikes in usage occur.